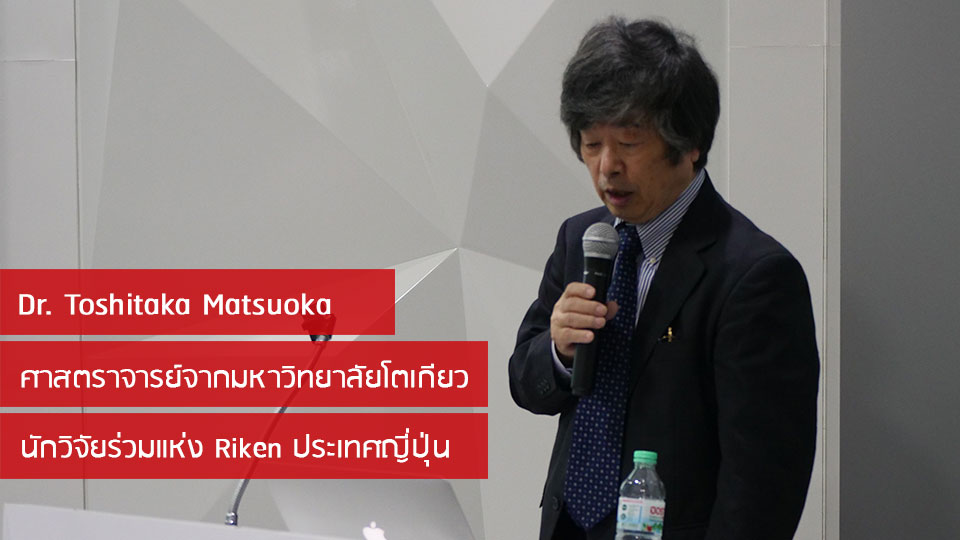
3 เทรนด์เทคโนโลยี สำหรับวงการผลิตชิ้นส่วน
เมื่อวันที่ 19 พฤศจิกายนที่ผ่านมา ในงานสัมมนา “The Latest Technical Trend Seminar” ซึ่งร่วมจัดโดย Factory Max, NS Tool, และ Sodick นั้น ได้รับเกียรติจากวิทยากรผู้ทรงคุณวุฒิ “Dr. Toshitaka Matsuoka” ศาสตราจารย์คณะวิศวกรรมศาสตร์ มหาวิทยาลัยโตเกียว และนักวิจัยร่วมแห่ง Riken สถาบันวิจัยที่ใหญ่ที่สุดแห่งประเทศญี่ปุ่น หนึ่งในผู้เชี่ยวชาญด้านเทคโนโลยีการผลิต ได้แสดงความเห็นต่อเทรนด์เทคโนโลยีงานกัด สำหรับอุตสาหกรรมผลิตชิ้นส่วนในยุคสารสนเทศไว้อย่างน่าสนใจ 3 ประเด็นหลัก ดังนี้
1. เครื่องจักรบนฐานของข้อมูล
ในยุคสารสนเทศหรือยุคแห่งข้อมูลนี้ การผลิตจะตั้งอยู่บนฐานของการรวบรวมข้อมูล เพื่อให้สามารถผลิตชิ้นงานได้อย่างเหมาะสมที่สุด ด้วยเหตุนี้เอง สิ่งที่ผู้ผลิตแต่ละรายจำเป็นต้องมี คือขุมข้อมูลของตน หรือโครงสร้างระบบคลาวด์สำหรับใช้ภายในบริษัท เพื่อยกระดับคุณภาพการผลิคของตนให้สูงขึ้น
ข้อมูลเหล่านี้จะส่งผลโดยตรงต่อการผลิต เนื่องจากเป็นปัจจัยที่เกี่ยวเนื่องกับเครื่องจักร และระบบอัตโนมัติ ว่าจะสามารถทำงานได้ดีมากน้อยเพียงใด ซึ่งหากมีข้อมูลที่ดีแล้ว เครื่องจักรก็จะสามารถทำงานได้อย่างมีประสิทธิภาพมากขึ้น ยกตัวอย่างเช่น หากเครื่องจักรเลือกใช้เครื่องมือที่เหมาะสมกับชิ้นงานได้เอง การผลิตก็จะรวดเร็วและตรงความต้องการขึ้นกว่าเดิม
โดยขุมข้อมูลนี้ ไม่ได้จำกัดอยู่เพียงแค่ข้อมูลจากคู่มือว่าวัสดุไหนต้องตั้งค่าเครื่องอย่างไร แต่จำเป็นต้องมีข้อมูลอื่น ๆ โดยละเอียด ไม่ว่าจะเป็นความยาวของเครื่องมือ ชนิดของวัสดุ ความเร็วรอบ สารหล่อเย็น หรือกระทั่งว่าในการทำงานนั้น ๆ เป็น Process ชนิดใด ซึ่งหากมีข้อมูลที่ละเอียดแล้ว เครื่องจักรก็จะสามารถเลือกได้อย่างถูกต้องว่าจะทำงานเช่นไร ใช้ Tools แบบไหน ทั้งหมดนี้เอง ที่จะทำให้เครื่องจักรฉลาดยิ่งขึ้น ส่งผลให้ได้มาซึ่งระบบการผลิตที่น่าเชื่อถือ และสามารถใช้งานได้จริง
นอกจากการนำข้อมูลมาใช้แล้ว ในอนาคต เครื่องจักรต่าง ๆ จะยังเชื่อมโยงกันมากยิ่งขึ้น หรือที่ในภาษาญี่ปุ่นเรียกว่า “Mieruka (การมองเห็นได้)” เพื่อให้สามารถตรวจสอบกระบวนการได้ในทุกขั้นตอน จากทุกสถานที่ รวมไปถึงการรวมกระบวนการทำงานต่าง ๆ ไว้ในระบบเดียวกัน เพื่อให้สามารถทำงานด้วยตัวเองได้ แม้กระทั่งอุปกรณ์ตรวจวัด ซึ่งจะกลายเป็นส่วนหนึ่งของระบบ เพื่อตรวจสอบว่าชิ้นงานที่กำลังจะทำงานในขั้นตอนถัดไปนั้นเหมาะสมแล้วหรือไม่ และทำการแก้ไขได้ด้วยตัวเอง
คุณสมบัติในการเชื่อมต่อกันเช่นนี้ ส่งผลให้ผู้ผลิตเครื่องจักรหลายรายเล็งเห็นว่า แผงควบคุมของเครื่องจักรแต่ละเครื่องจะกลายเป็นสิ่งที่ไม่จำเป็น และอยู่ระหว่างการพัฒนาระบบควบคุมด้วยสมาร์ทโฟน หรือแท็บเล็ต ซึ่งเป็นอุปกรณ์ที่หาได้ง่าย และใช้งานได้สะดวก รวมถึงสามารถควบคุมจากทางไกลได้
ในระยะเริ่มต้น ผู้ใช้เครื่องจักรสามารถติดตั้งอุปกรณ์เพิ่มเติม เพื่อให้เครื่องจักรที่ตนมีอยู่เดิมสามารถเชื่อมต่อเข้ากับเครื่องจักรอื่น ๆ ได้ อย่างไรก็ตาม ในอนาคต หรือผู้ที่ต้องการความแม่นยำในการทำงานมากขึ้น อาจมีความจำเป็นต้องพิจารณาซื้อเครื่องจักรใหม่ เพื่อรองรับกับการทำงานในยุคแห่งข้อมูลเช่นนี้ต่อไป
2. เทคโนโลยี Endmill
ปัจจุบัน Endmill คือสิ่งที่มีความสำคัญในการผลิตชิ้นงานเป็นอย่างยิ่ง โดยเฉพาะในช่วงหลังมานี้ อุตสาหกรรมสมาร์ทโฟนและอากาศยานเติบโตขึ้นอย่างรวดเร็ว มีการเปลี่ยนแปลงวัสดุที่ใช้ในการผลิต เช่น การนำสเตนเลสมาใช้ในชิ้นส่วนสมาร์ทโฟน รวมถึงการเกิดขึ้นของวัสดุชนิดใหม่ ๆ อย่างต่อเนื่อง เช่น Inconel (โลหะผสมนิเกิ้ลอัลลอยด์), CFRP (Carbon fiber reinforced polymer) เป็นต้น ส่งผลให้การพัฒนา Endmill กลับมาเป็นเทรนด์ที่ผู้ผลิตหลายรายต่างวิจัย เพื่อให้เหมาะสมกับการกัดชิ้นงานตามความต้องการของตลาดยิ่งขึ้น
ที่แล้วมา ดอกกัดสำหรับงานเซาะร่องมักเป็นแบบ 2 คมกัด แต่ในอนาคต การพัฒนา Endmill จะมุ่งเน้นไปที่ 2 ข้อหลัก ๆ ดังนี้
- การพัฒนาให้สามารถทำงานแบบ High Feed
- การเปลี่ยนรูปทรงของ Endmill ให้เหมาะสมกับเครื่อง 5 แกน
ทั้ง 2 ข้อนี้ คือการพัฒนาเพื่อให้กัดชิ้นงานได้อย่างมีประสิทธิภาพสูงสุด การกัดงานด้วย Endmill แบบดั้งเดิมนั้น จุดกึ่งกลางของ Endmill ไม่มีการกัดเฉือน หรือมี Vc = 0
Dr. Matsuoka จึงมีความคิดว่า หากเปลี่ยนวิธีการกัด จากเดิมที่กัดเป็นมุมฉาก มาใช้ส่วนขอบแทน และเพิ่มจำนวนฟันให้มากขึ้น ก็จะสามารถลดขนาดเศษให้เล็กลง ซึ่งจะทำงานได้เร็วขึ้น อีกทั้งยังลดปัญหาที่เกิดกับตัวเครื่องได้อีกด้วย
จากการทดลอง พบว่า การกัดงานที่ขอบนอกเป็นมุมเฉียงซึ่งมี Vc สูง ทำให้เกิดการสึกหรอของ Endmill ลดลง ดังนั้น Endmill จึงมีอายุการใช้งานที่ยาวนานยิ่งขึ้น
ปัจจุบัน ผู้ผลิตต่างเร่งพัฒนา Endmill ให้มีค่าที่เหมาะสมต่อการทำงานมากยิ่งขึ้น โดย Dr. Matsuoka ได้พัฒนา Endmill ที่มีคุณสมบัติในการกัดที่ความเร็วรอบสูง แต่มีความแม่นยำ และลักษณะผิวงานที่ดียิ่งขึ้น โดยการทดลองทำงานเปรียบเทียบกันระหว่าง Endmill แบบ 2 ฟัน และแบบ 4 ฟัน พบว่า Endmill แบบ 4 ฟัน สามารถกัดงานแบบเดียวกันได้ด้วยระยะเวลาเพียงครึ่งหนึ่งของแบบ 2 ฟัน อีกทั้งมีการสึกหรอน้อยกว่าตามที่ Dr. Matsuoka คาดคิด
นอกจากนี้ ในส่วนของการกัดงานที่มีความเหนียวสูง เช่น อะลูมิเนียม ทองแดง และอื่น ๆ นั้น แม้ว่าจะเป็นชิ้นงานที่สามารถทำงานได้ง่าย อย่างไรก็ตาม ยังคงมีปัญหาในส่วนของพื้นผิวชิ้นงาน ซึ่งหากใช้คมกัดที่มีความคมมากเป็นพิเศษ และควบคุมให้สามารถกัดงานอย่างแม่นยำขึ้นแล้ว จะสามารถกัดชิ้นงานให้เกิดครีบได้น้อยลงเป็นอย่างมากอีกด้วย
นอกจากนี้ Dr. Matsuoka ยังได้แนะนำเพิ่มเติมว่า ในการกัดสเตนเลส เมื่อใช้ความเร็วตัดสูงที่ 200 เมตรต่อนาที (Vc 200) จะให้ผลลัพธ์ที่ดีที่สุด เนื่องจากผลลัพธ์ที่ได้จากการกัดด้วย Vc ต่ำนั้นแทบไม่ต่างกัน ทั้งชิ้นงาน และการสึกหรอของเครื่องมือ อย่างไรก็ตาม การกัดด้วยความเร็วสูงนี้ ทำให้สามารถทำงานได้เร็วขึ้นเป็นอย่างมาก
3. เครื่อง 5 แกน คือ อนาคต
ปัจจุบัน เครื่องจักรที่มีการใช้งานอย่างแพร่หลาย คือเครื่อง 3 แกน อย่างไรก็ตาม Dr. Matsuoka กล่าวแสดงความเห็นว่า ในอนาคต เครื่อง 5 แกนจะกลายเป็นเทรนด์หลัก และเข้าแทนที่เครื่อง 3 แกนในปัจจุบันทั้งหมดในท้ายที่สุด
ปัจจัยสำคัญ ที่จะทำให้เครื่อง 5 แกน เข้ามาแทนที่เครื่อง 3 แกน คือ “ความยาวของ Endmill” ซึ่งเครื่อง 5 แกน ใช้ Endmill ที่สั้นกว่าเครื่อง 3 แกน ทำให้เครื่องสามารถจับ Tools ได้อย่างมั่นคง ลดการโก่งของ Tools และใช้ความเร็วที่สูงขึ้นในการทำงานได้ นอกจากนี้ ด้วยโครงสร้างของตัวเครื่องที่สามารถปรับมุมของชิ้นงานได้อย่างอิสระ ทำให้สามารถใช้ Endmill ที่สั้นลงในการกัดชิ้นงานได้ลึกและทั่วถึงกว่าเดิมอีกด้วย
อีกสิ่งสำคัญ คือ เครื่อง 5 แกนเหมาะกับชิ้นงานที่ต้องกัดจากหลายด้าน ซึ่งต่างจากเครื่อง 3 แกนที่ต้องถอดชิ้นงานออกมาเปลี่ยนทิศอีกด้วย
ด้วยเหตุนี้เอง ในผู้ผลิต Cutting Tools จึงเร่งพัฒนา Endmill ที่มีความยาวน้อย คมกัดสั้นลง แต่มีจำนวนคมกัดมากขึ้น และไม่มีคมกัดที่จุดศูนย์กลาง เพื่อให้สามาถกัดงานได้เร็วมากยิ่งขึ้นไปอีก โดยตั้งเป้าเพื่อใช้งานกับเครื่อง 5 แกนโดยเฉพาะ คาดการณ์ว่า หน้าตาของ Endmill สำหรับเครื่อง 5 แกนในอนาคต จะต่างไปจากในปัจจุบันเป็นอย่างมาก เพื่อให้รองรับกับการกัดชิ้นงานในมุมเอียงที่ต่างกันไป
Dr. Matsuoka กล่าวเสริมว่า แม้ในการทดลอง จะใช้ CAM ที่พัฒนาขึ้นเอง เพื่อให้ได้ผลลัพธ์สูงสุด และการโปรแกรมสำหรับเครื่อง 5 แกนนั้นทำได้ยากกว่าเครื่อง 3 แกน อย่างไรก็ตาม ขณะนี้ผู้ผลิตหลายราย ต่างให้ความสำคัญกับเครื่อง 5 แกนมากยิ่งขึ้น โดยพัฒนาซอฟต์แวร์เพื่อให้สามารถทำงานที่ยุ่งยากนี้ให้ง่ายลงได้ จึงไม่จำเป็นต้องเป็นกังวลกับความคืบหน้าในการพัฒนาเทคโนโลยีของแต่ละฝ่ายที่เกี่ยวข้องแต่อย่างใด