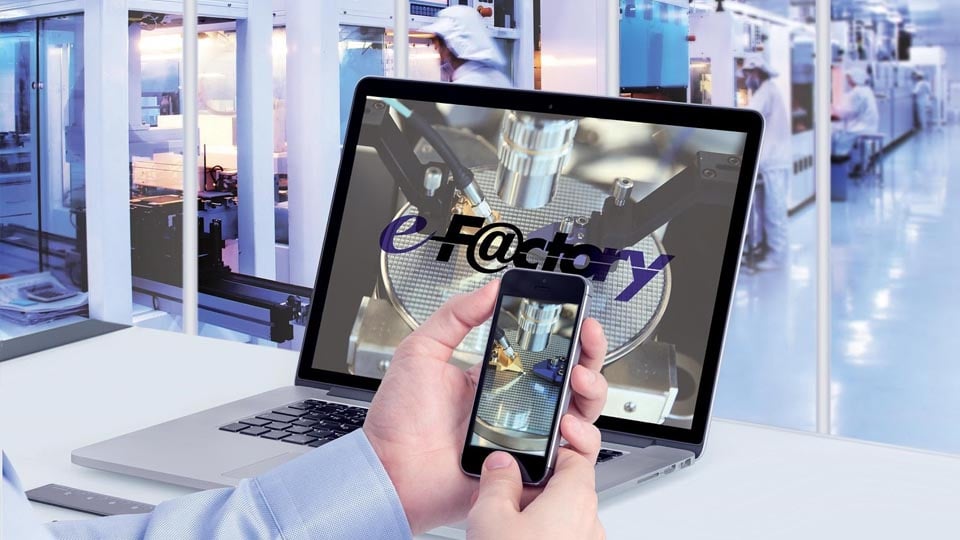
การปรับปรุงประสิทธิภาพการผลิตในยุคอุตสาหกรรม 4.0
ปัจจุบัน สังคมไทยกำลังเข้าสู่สังคมผู้สูงอายุ ซึ่งในอนาคตอาจทำให้เกิดปัญหาขาดแคลนแรงงานและค่าใช้จ่ายด้านแรงงาน รวมไปถึงการแข่งขันที่สูงมากขึ้นในอุตสาหกรรม เพื่อความอยู่รอดในสถานการณ์ดังกล่าว ผู้ประกอบการจึงจำเป็นที่จะต้องเริ่มต้นปรับตัว โดยมีการจัดการและวางแผนการใช้ทรัพยากรที่มีอยู่ให้เกิดประสิทธิภาพสูงสุด ซึ่งจำเป็นต้องมีการเก็บรวบรวมข้อมูลการผลิตและนำมาวิเคราะห์อย่างรวดเร็วเพื่อการตัดสินใจที่ทันต่อสถานการณ์
การปรับปรุงสู่โรงงานอัจฉริยะ (Smart Factory) จึงเป็นทางเลือกที่ตอบโจทย์ เนื่องจากการนำ IoT มาใช้ทำให้สามารถมองเห็นโรงงานของตนเองได้ตั้งแต่กระบวนการผลิตไปจนถึง Supply chain และติดตามสถานะของอุปกรณ์ต่างๆในโรงงานได้ในแบบ real-time ซึ่งช่วยเพิ่มประสิทธิภาพการผลิต ลดต้นทุน TCO (Total cost of Ownership) ลดระยะเวลา downtime และข้อบกพร่องในกระบวนการผลิต และทำให้ประหยัดพลังงานยิ่งขึ้น โดย มิตซูบิชิ อีเล็คทริค ได้แนะนำขั้นตอนการปรับปรุงประสิทธิภาพดังนี้
1. วิเคราะห์กระบวนการผลิต
เพื่อที่จะปรับปรุงประสิทธิภาพการผลิต ผู้ประกอบการจำเป็นต้องรู้และเข้าใจกระบวนการผลิตของตนเองก่อน ไม่เช่นนั้นจะไม่สามารถแก้ไขได้อย่างตรงจุด และสิ่งที่ลงทุนไปอาจเสียเปล่า
สำหรับการวิเคราะห์ปัญหาในกระบวนการผลิต แนะนำให้ใช้ Edge computing solution ซึ่งเป็นการดึงข้อมูลการผลิตจากหน้าไซต์งานและประมวลผลเพื่อส่งไปยังระบบ IT ในสำนักงาน ซึ่งอาจติดตั้งโมดูล High-Speed Data logger เพื่อเป็นตัวกลางในการรวบรวมข้อมูลต่างๆ เช่น ข้อมูล Cycle time ตัวแปรที่ใช้ในการผลิต หรือระยะเวลาที่ใช้ในการผลิตชิ้นงาน และติดตั้งเซ็นเซอร์ที่เหมาะสมเพื่อตรวจสอบคุณภาพของชิ้นงาน หรือติดตั้งโมดูล Energy Measuring เพื่อเก็บค่าพลังงานในการผลิต นอกจากนี้ควรตรวจสอบเพื่อแบ่งแยกงานที่ไม่เหมาะกับมนุษย์ เช่น งานที่ต้องทำซ้ำๆ งานที่ต้องใช้ความละเอียดสูง และงานที่ต้องยกของหนัก
2. หาโซลูชั่นเพื่อแก้ปัญหา โดยใช้ระบบอัตโนมัติเพื่อช่วยปรับปรุงประสิทธิภาพการผลิต
หลังจากที่ผู้ประกอบการสามารถระบุปัญหาและสาเหตุได้แล้ว ขั้นตอนต่อไปคือการแก้ไขปัญหาที่พบ โดยยกตัวอย่างปัญหาหลักๆ ดังนี้
● ระยะเวลาที่ใช้ในการผลิตและความผิดพลาดจากมนุษย์
- ปรับปรุงการผลิตโดยใช้ระบบอัตโนมัติ เช่น พีแอลซี หน้าจอสั่งการระบบสัมผัส
- ใช้ระบบสายพานในการขับเคลื่อนชิ้นงาน
- ใช้โรบอตในงานที่ไม่เหมาะสมกับมนุษย์
● คุณภาพของผลิตภัณฑ์
- ตรวจสอบคุณภาพโดยใช้กล้อง vision หรือเซ็นเซอร์ที่เหมาะสม
- ใช้เซอร์โวในงานที่ต้องการความแม่นยำสูง
- ใช้ข้อมูลที่บันทึกไว้เพื่อตรวจสอบหาการทำงานที่ผิดพลาด หรือการตั้งค่าตัวแปรที่ไม่ถูกต้อง
● การใช้พลังงาน
- ใช้อินเวอร์เตอร์ในการควบคุมพัดลมและปั๊ม
- ใช้ระบบ SCADA ที่ช่วยในด้าน visualization ช่วยให้มองเห็นกระบวนการผลิตและควบคุมได้ในแบบ real-time สามารถดูค่าประสิทธิภาพโดยรวมของโรงงาน (OEE) รวมไปถึงค่าการใช้พลังงาน นอกจากนี้ยังสามารถกำหนดตารางการทำงานของเครื่องจักรเพื่อลดการใช้พลังงานได้อีกด้วย
3. ตรวจสอบ ประเมินและปรับปรุง
ขั้นตอนสุดท้ายหลังจากปรับปรุงกระบวนการ ควรทำการตรวจสอบและประเมินผล โดยอาจใช้รายงานเปรียบเทียบค่าระหว่างก่อน-หลังทำการปรับปรุงเพื่อพิจารณาความคุ้มค่า ซึ่งการปรับปรุงสู่โรงงานอัจฉริยะ (Smart Factory) ไม่จำเป็นที่จะต้องทำทั้งหมดในคราวเดียว ควรเริ่มจากกระบวนการหนึ่งๆก่อน และเมื่อเห็นผลประสิทธิภาพแล้วจึงค่อยประยุกต์กับกระบวนการอื่นๆต่อไปตามความเหมาะสม โดยควรทำการตรวจสอบและปรับปรุงอยู่เสมอเพื่อพัฒนากระบวนการผลิตให้โรงงานค่อยๆเข้าสู่ความเป็นอัจฉริยะมากขึ้น เพื่อแก้ไขปัญหาต่างๆ และช่วยในการจัดการทรัพยากรให้เกิดประสิทธิภาพสูงสุด