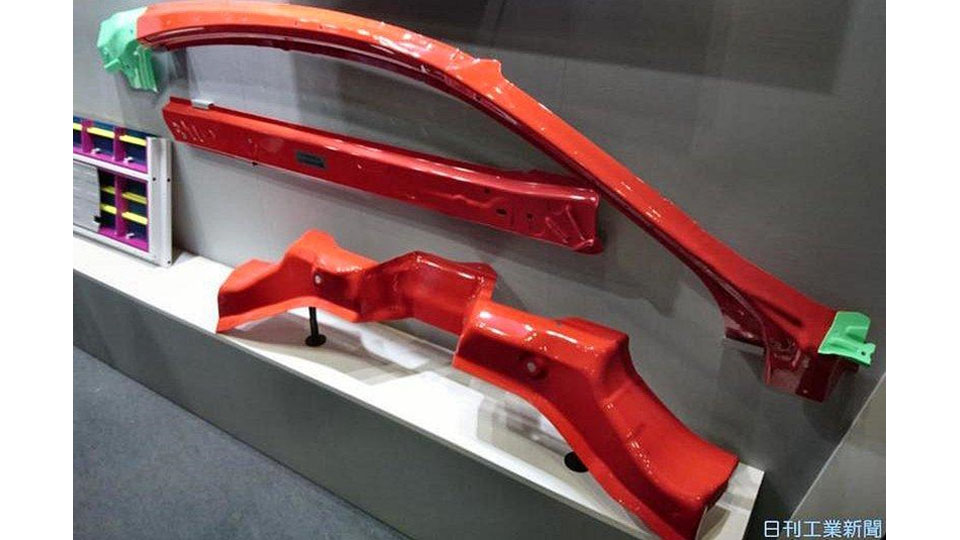
Hot Stamping Used In Parts Production To Reduce Vehicle’s Weight
Many auto manufacturers are developing their hot stamping technique (hot-forming) in order to serve the popular use of ultra high tensile steel and the dramatically increasing utilization of other high quality materials, following the vehicle weight reduction demand of the manufacturers. In the meantime, Gestamp Automoción, a Spanish company and one of the world’s largest part manufacturers has decided to open a new plant in Japan to enhance its competitiveness in the auto parts market with its capability to work with new materials.
In addition, FUTABA INDUSTRIAL, an auto part manufacturer under Toyota Group has placed an investment of 10,500 million yen in additional production lines of hot stamping machines at Kota plant in Aichi prefecture of Japan, and at a plant in Canada, leading to an increase of 6 production belts, the numbers of which are equivalent to those of Mutsumi plant in Okazaki, Aichi prefecture, which are to serve Toyota’s new vehicle models.
Hot stamping technique is a hot-forming method which is very popular in Europe where 30-40% of the vehicle’s body are produced with the technique. It is suitable for forming high-strength materials and it provides variety of forming strength. Mr. Yoshiyuki Nakanishi, the Director of FUTABA INDUSTRIAL, said that “the present demand of the parts produced by the hot stamping technique is gradually rising since the cold press technique (cold-forming) is used for forming more complicated parts.”
On the other hand, an effort to develop the forming of ultra high tensile steel with cold press technique is in progress. In March, Toyoda Iron Works announced the increase of the 3,000-ton cold press machines at Nukata plant.
In addition, Toyoda Iron Works ordered more hot stamping machines to be installed at the plants in Japan, the United States, Turkey, and China. Chairman Kazuhiko Takarada said that it was “a preparation for the part manufacturing of the two methods” and there was a plan for additional investments in the future. While ASKA, an important trading partner of Mitsubishi Motors, also has planned an additional installation of the 3,500-tonne cold press machines in October at its major plant in Kariya, Aichi prefecture.
It is worth noting that these companies have followed the same direction of Gestamp Automoción whose 12.5% of the total investment in infrastructure development acceleration project in Japan was financed by Mitsui Group. A new plant of Gestamp Automoción will be built in Matsusaka, Mie prefecture, with the commencement of production in August to September and it is the first time the company has decided to built its plant in Japan. The company opined that “its hot stamping process will be developed for high quality in order to be different from those of other companies in Japan.”
The auto weight reduction demand came from the overweight parts of motors and batteries of EV. It is expected that the vehicle weight reduction will be more widespread. Nowadays, aluminum and carbon fiber are used by many companies who are developing the vehicle weight reduction technology of more advanced hot stamping technique in the future.