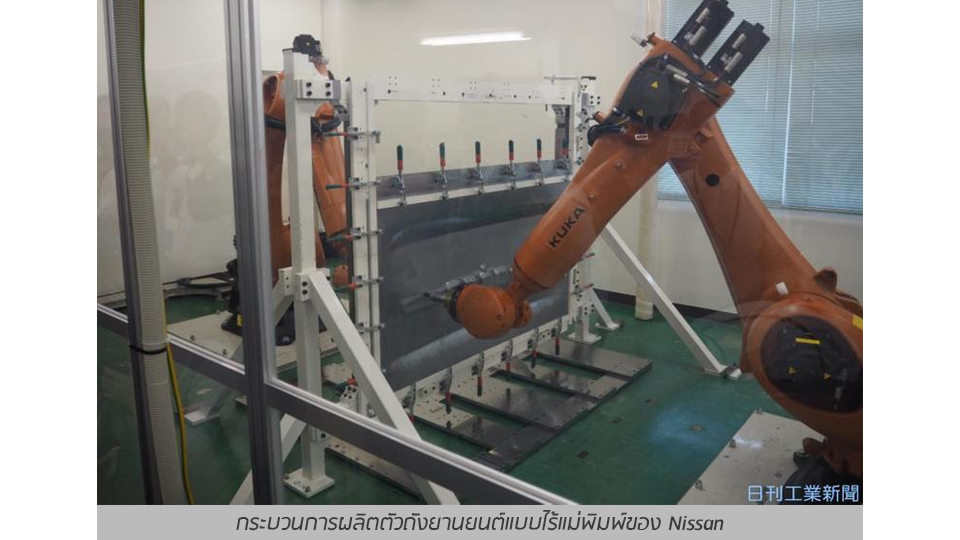
Die-Less Moulding - Nissan Automotive Body Panels Manufacturing Technology with Robot
On 2 October 2019, Nissan Automotive announced its successful development of the die-less manufacturing technology for automotive body panels, in which robotic arms with cylindrical tools are used. This technique will serve various forms of body panels manufacturing and is highly suitable for high-mix low-volume parts manufacturing while it requires only 10% of the machine cost. Nissan aims to use this technology to manufacture car accessories and parts for older model cars that have been discontinued as well as has plans to implement it in the general production lines in the future.
The vice president of Nissan Mr. Hideyuki Sakamoto said that this production technology is called "Incremental Forming". It starts with shaping the parts into 3D data and then using the robot arm equipped with cylindrical tools to roughly shape the parts before using other two robots, one in the front and the other in the back, to shape the parts into the desired shape. After that, put the obtained parts to a gripping device to finish the job as the final step. Currently, no car makers use this technology to manufacture their cars yet.
Generally, automotive body panels are manufactured by using the compression moulding method, which is suitable for mass production because of its low cost. However, it is not worth the mould in manufacturing parts of small quantity.
This new method will cost 100,000 to 1,000,000 yen for the equipment and design costs. It can be used with normal production robotic arms and has a lead time of 3 to 28 days, as opposed to the compression moulding method that possibly requires a one-year lead time when the process of the mould design is also accounted for.