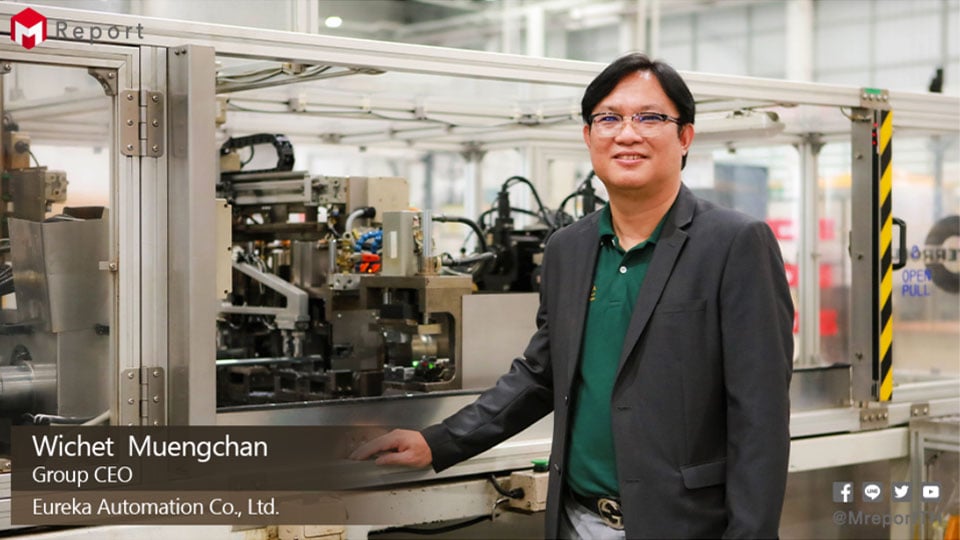
Uncover the idea behind Eureka Automation's special machine design that becomes the powerhouse of Interroll Thailand's plant
Let’s dig into the idea behind Eureka Automation's specialized machine design and build that becomes the powerhouse at Interroll Thailand's plant, the world class brand of belt rollers.
Mr. Wichet Muengchan, group CEO of Eureka Automation Co., Ltd., and Mr. Grisorn Nakapong, Managing Director of Interroll (Thailand) Co., Ltd., participated in discussions with M Report on specialized machines created in-house to replace imported equipment from abroad. Ready to tour the Interroll Thailand factory in Amata City, Chonburi, the sole production facility in ASEAN?
Beginning of Special Machine at Interroll Thailand Factory
According to Mr. Wichet, upon learning the customer’s needs, it is necessary to take into account the workpiece quality requirements, which crucially include the work process and the factors of the work process, as well as to figure out what are the pain points for customers. This is the starting point for finding solutions. Though the production line of automation at Interroll’s plant seems to be a simple design, there is some subtle intricacy in it. Since each modular conveyor platform is custom-made according to customer’s specifications, the machinery must therefore be designed to accommodate all kinds of diversity of the workpiece production.
Mr. Graisorn describes the former batch manufacturing facility of Interroll, where the production line was set up in accordance with the procedure, moving from one step to the next. It includes cutting shafts, drilling holes, grooving, tapping, and assembling parts; however, some orders may omit some steps.
Although the prior factory's batch production satisfies the requirements for manufacturing custom-made products, it has a flaw in terms of quality control. Particularly when there is a product defect, the entire batch is often defective, causing it to have to remanufacture the whole thing, or the bad quality is not noticed until after the product has been utilized.
When Interroll had the chance to increase investment in Thailand in 2019, it relocated to a new 5,000 square meter factory in the Amata City Industrial Estate, Chonburi, with three times more production capacity. In order to respond to business expansion and plan for increased production efficiency, speed, accuracy, and faultless quality, automated machinery similar to that found at the Interroll factory in Germany is needed.
However, it was determined that importing such machinery is not worth the expenditure when taking into account the output volume. Therefore, Interroll looked for a machine maker in Thailand to design and build a machine customized for the Interroll Thailand production line with a focus on making it easy to use, flexible, and able to precisely control various factors.
Three main questions in special machine design
The following three major issues about the design of this machine were raised during discussions between the two alliances:
Combine process : integrate process into one machine
Because Interroll's production volume determines takt time (production speed) and cycle time (machine speed), Eureka Automation develops a special machine that combines five processes, changing from batch production to one-piece flow. So instead of producing the workpiece one process at a time and waiting until the number of batches is complete before moving on to the next process, the workpiece is put through the machine one at a time and gets the finished product continuously.
In traditional manufacturing, the procedures must be followed step by step, which require multiple machines and operators. By combining all five processes into one machine, each workpiece can be quickly manufactured in a short time with perfect quality.
Tool life management : quality & effectiveness
The key component of the machine is tooling, which is a tool used to mill or drill the workpiece. It is necessary to have quality control because it directly affects the quality of the workpiece. The tool will gradually wear or deteriorate according to its use. Using expired or deteriorated tools will lead to waste. On the other hand, replacing unexpired tools is wasteful. In order to preserve quality and maximize the utility of the tool, the machine must incorporate a warning system to replace the tool when it is no longer usable.
Tool change over and error proofing : Poka-yoke system
The inability to drill holes in the center, inadequate thread tapping, the use of the wrong tool or workpiece, and other quality control process pain points need the creation of an error-proofing system known as a poka-yoke to prevent human error. The machine must be easily set up to manufacture workpieces of various sizes, cutting down on production time and increasing accuracy. For control, it requires sensors and software that can detect errors and immediately notify the operator if anything is off. Time lost and production waste are greatly decreased as a result.
All three issues have been solved by creating an automated special machine that operates cutting shafts, drilling holes, beveling, chamfering, and blowing dust. Sensors are used to monitor a variety of operations, such as whether or not the tool matches the size of the workpiece to be produced. If it is wrong, the machine won't work until the personnel makes the necessary corrections. This can effectively avoid production errors.
Additionally, even though this machine may perform a variety of processes, not all processes must be finished. You can choose to only select the processes you need, such as just drilling and tapping holes. It largely fulfills the requirements for creating customized products.
Interroll Thailand now employs a total of three specialized machines developed and produced by Eureka Automation and can handle workpieces with various requirements, Mr. Graisorn disclosed that Interroll Thailand is developing a more automated production system. The manufacturing process has not yet been entirely streamlined and perfectly automated.
Eureka Automation: a Thai SI developer and manufacturer of machinery and automation systems
Despite the fact that system integrator is a relatively new career in Thailand that has emerged along with the boom in robotics and automation systems in Thai factories, Thai SI company Eureka Automation has 20 years of industry experience and exports machines to clients in 15 different countries around the world.
Mr. Wichet disclosed that Eureka Automation was founded as a developer and manufacturer of specialized machines for the production process that were both semi- and completely automated. The automotive industry served as the primary market at first. As the industry turned to robotics and automation to boost production efficiency, Eureka Automation’s mission as a SI began. The customer base has grown to include groups other than automotives, for example, distribution center warehouses, factories, automated production equipment in food processing facilities, electrical and electronic companies, and others.
Eureka Automation's strength is its commitment to its clients and business partners. Its specialty is developing and constructing automated machines or systems for various processes, including assembly process (80% of the total), testing process, automatic moving or storing process, and other processes customized to fit customer’s needs.
Getting to know Interroll, the world’s most recognizable belt roller brand
Interroll is a world-famous brand of belt rollers that we may have used without knowing it. It is an important component in conveying various products in distribution centers such as 7-Eleven convenience stores or even luggage conveyor belts at Suvarnabhumi Airport.
These conveyor belt rollers, which Mr. Graisorn refers to as modular conveyor platforms (MCPs), allow for design flexibility. They can be modified and reconfigured in a variety of ways. Like a jigsaw puzzle, MCPs can be installed fast and easily, greatly facilitating the system integrator in designing and installing the conveyor system.
Since 1993, Interroll has operated in Thailand as "Interroll (Thailand) Company Limited." It initially imported goods for local sale until it started the production line by using some local content. In 2019, it relocated to the new plant at Amata City Industrial Estate, Chonburi, in order to keep up with anticipated development brought on by the EEC, Southeast Asia, and the automation of labor.
Interroll Thailand’s plant is the only production facility in ASEAN and one of the three in Asia.