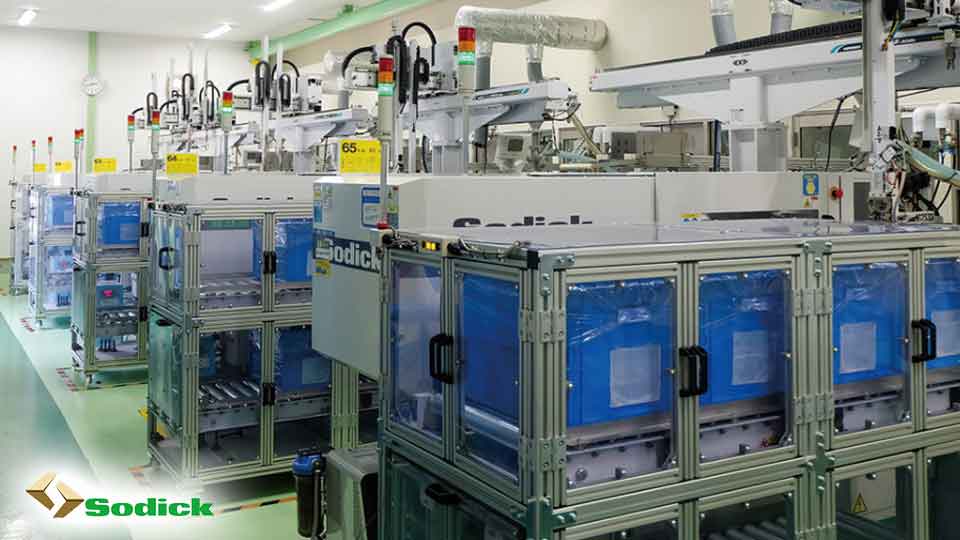
Sodick released Fineplas Interview: Challenging New Technology, Metal 3D Printing and Automation support more sophisticated in-vehicle parts
Sodick released Fineplas interview on metal 3D printing and automation, the challenging new technology that is ahead of the times, to support more sophisticated in-vehicle parts
Metal 3D printing and automation support more sophisticated in-vehicle parts
The electrification of automobiles is forcing parts manufacturers to make major changes. One of these is in-vehicle plastic parts. Molds and molding technology are becoming more sophisticated due to increasingly narrow connector pitches and the adoption of highly heat-resistant resins. Fineplas handles everything from mold making to molding and assembling in-vehicle parts such as connectors. They are growing orders by responding to increasingly sophisticated requirements through the utilization of metal 3D printers and automated molding lines.
The company was founded in 1967 and started as a manufacturer of plastic parts. At that time, they handled a wide range of domestic appliances and household goods as well as automobiles but decided to specialize in automobiles in the latter half of the 1980s.
The reason was the expansion of their customers overseas. Based on his own experience, Chairman Kojiro Sammiya, who previously worked for an electronic parts manufacturer, said, “Household appliance manufacturers are rapidly moving overseas, which makes things more difficult. So, we decided to shift into the automobile field that was growing in Japan. We concentrated all management resources on electrical components for automobiles.”
They were particularly conscious of “stabilizing quality.” This is because the automobile field demands more stable quality than other fields. In the early 1990s, the company introduced a Sodick injection molding machine which was newly developed at that time. Its ability to successfully mass produce polyphenylene sulfide (PPS) parts with a 0.3 mm wall thickness was recognized by electrical equipment manufacturers and presented a big opportunity to strengthen the company’s involvement in automobiles.
Another thing they were conscious of was keeping production in-house to handle everything from mold making to molding and assembly.
Since his time in his previous job, Chairman Sammiya has believed that in-house production is essential to maintain competitiveness, and he has strengthened the system for mold design and production, molding, and assembly.
Mold-making changes due to narrower pitches and heat-resistant resins
The company has been specializing in in-vehicle resin parts since the 1980s and has continued to grow its business performance. However, it is said that parts manufacturing has changed in recent years because of the increased sophistication of automobiles due to factors such as electrification.
One of these is narrower connector pitches. “The weight of molded products is about half that of 20 years ago, at the same level as household appliances,” said Chairman Sammiya. For example, the terminal size for in-vehicle connectors is 0.64 mm and the pitch will be narrower in the future.
One of the major changes is the increase in the number of highly heat-resistant resins. Semi-aromatic polyamide resins such as Nylon 6T are becoming more common. As these materials generate a large amount of gas, it is important to vent the gas and discharge the gas from the cavity.
“Because of the demand for thinner walls, we have to review the structure of the mold,” said Kenki Takami, technical advisor to the Manufacturing Division.
In-vehicle connectors with 0.64 mm terminal size
The mold decides 90%
Chairman Sammiya's theory is that “the mold determines at least 90% of a molded product’s quality.” This is because increasing precision and miniaturization make adjustments at the molding stage more difficult. Recent advances in miniaturization create an increasing demand for molds that are more compact and permit high-cycle molding.
The use of metal 3D printers to create such molds has been growing in recent years. Sodick OPM250L metal 3D printers were introduced into the group companies in 2019. They manufacture molds with a structure that emphasizes cooling of the sprue runner part where the temperature is highest and have cooling circuits arranged at equal distances from the insert. Adopting the optimal cooling structure achieves more compact molds and more stable molding quality.
Recently, metal 3D printers have been used to manufacture the molds for the connector core pins. Approximately 1 mm diameter cooling circuits are formed inside.
“Since water cooling is difficult at this scale, we adopted air cooling,” says Tsuyoshi Hayakawa, Deputy Chief of Mold Development Section, Technology Development Division.
This achieved more stable quality (dimensional accuracy and deformation prevention), leading to a halving of the molding cycle.
Mold with internal air-cooled structure
Pursuing stable product quality through automation
In addition to developing molds for metal 3D printers, they are currently working on unmanned and automated molding lines. The aim is to further improve the quality.
“We are proceeding with PPM management but still need to reduce the anxiety factor caused by human intervention as much as possible, so we have promoted automation,” says Chairman Sammiya.
The automation line where the latest 11 molding machines are lined up is not only constant-temperature controlled but temperature changes are suppressed as much as possible by separating the molding and drying processes.
In addition, as the person in charge is alerted when a problem occurs, the line operates without human intervention except for sample inspections once every four hours. “The rate of defects has become overwhelmingly low. But there is still room for improvement, so we will proceed with further automation,”says Mr Takami, the Technical Advisor.
Into an era of co-creation
In regard to future technological trends, Chairman Sammiya pointed out that, “technological development by a single company is going to be difficult.” He anticipates that this will be an era when co-creation is necessary, saying “We need to go forward with makers of machines, molds, parts, and materials. Although we haven't achieved it yet, it would be nice to have cross-company projects and study sessions.”