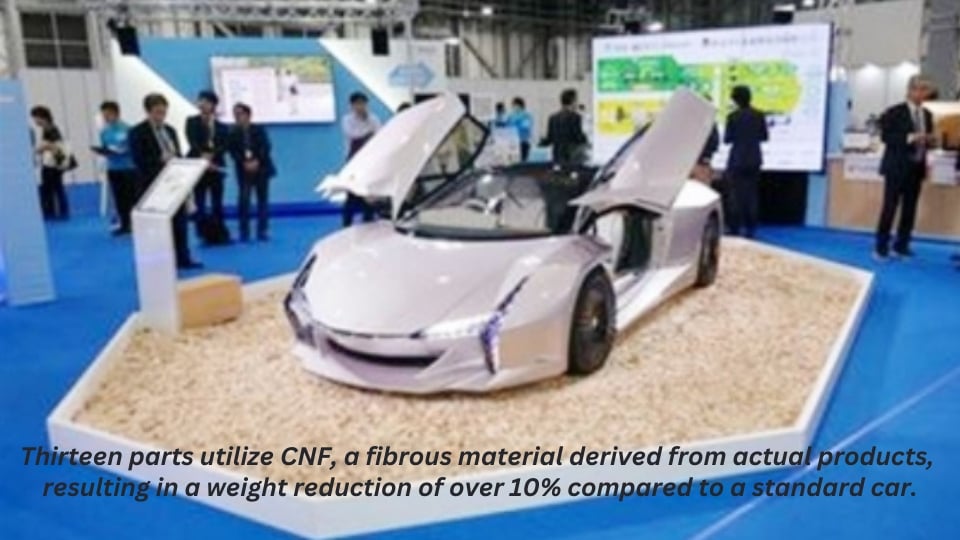
The Awakening of the Cellulose Nanofiber Market: Boosting Decarbonization with a Plant-Based, Light, and Strong Material
Cellulose nanofiber (CNF) is a plant-based material as strong as iron but lighter. It is expected to reduce the consumption of fossil resources and expand the recycling of plastics.
Japan, Dec 8, 2023 - Professor Hiroyuki Yano of Kyoto University’s Institute for Sustainable Humanosphere, who has been researching CNF for many years, said, “CNF is the fourth material that will support industry in the 21st century, and there is a large market for it.”
CNF is made from cellulose, which is the main component of plants. The process is the same as papermaking until the wood chips are crushed, melted, and turned into pulp. When the pulp is finely disentangled and made into nano (one-billionth) size, it becomes CNF. It is one-fifth as light as steel but five times stronger. Since it is derived from plants, it has less environmental impact. Professor Yano emphasizes, 'All plants have cellulose, and Japan being a forested country means an abundance of raw materials.'"
It has been put into practical use in some areas, and is useful in preventing stickiness in cosmetics, improving the smoothness of ink, and deodorizing diapers. Another promising use is as a plastic reinforcement material.
By mixing small amounts of CNF with resin, it is possible to create stronger plastic that can be made thinner and lighter without sacrificing the lightness of plastic. If used in automobile parts, it can reduce the weight of the car body, improve fuel efficiency, and reduce carbon dioxide (CO2) emissions during driving.
In 2001, Professor Yano mixed CNF with resin to develop a material with strength comparable to steel. In 2005, he collaborated with the Ministry of Economy, Trade and Industry, the Kyoto City Institute of Industrial Science and Technology, and companies to establish the “Kyoto Process,” a direct kneading method for mixing pulp with resin and turning it into CNF. Normally, plastic and plants do not mix easily, but they succeeded in evenly distributing CNF into the resin. The process could be omitted and manufacturing costs could be reduced.
In 2018, ASICS adopted CNF composite cushioning in its shoes. This cushion material is mass-produced by Seiko PMC using the Kyoto process and is lightweight and durable. At the 2019 Tokyo Motor Show, the results of the Kyoto process were used in a sports car prototypeed by the Ministry of the Environment. The car body's weight has been reduced by 16%, and fuel efficiency has improved by 11%.
In August 2023, Yamaha Motor Co., Ltd. announced that it had adopted CNF for the engine cover of its watercraft to be sold in North America. Nippon Paper Industries supplied the material, mixed with CNF to increase its strength.
Watercraft engine cover reinforced with CNF material (Yamaha Motor)
Attention for recycling: Remolding waste plastic, expanding its use
As CNF continues to build up its track record, it is also attracting attention as a material that will expand plastic recycling. Typical recycling involves pulverizing waste plastic collected from products, melting it, and molding it into new products. However, the uses of waste plastics are limited because they are susceptible to deterioration. Mixing CNF during remolding increases the strength of even waste plastic, expanding the range of uses for recycled materials.
Although a low-cost manufacturing method has been found using the Kyoto process, Professor Yano stated, 'It's still expensive, considering the volume of its use in Zone 7,” Professor Yano said. Therefore, one option is micro (one-millionth) size cellulose fiber. Not only can manufacturing costs be reduced because the resin is not miniaturized to the nano level, but the content in the resin can be increased 2 to 3 times, reducing the use of fossil resources and reducing CO2 emissions. However, since it is a plastic that easily absorbs moisture, Mr. Yano says “There should be different ways to use it depending on the needs of the user.”
Professor Yano has been researching CNF for nearly a quarter of a century. “In the 20th century, metals, ceramics, and plastics supported industry. In the 21st century, ‘structural CNF’ supports industry as the ‘fourth material.’ Originally made by absorbing CO2, it is also recyclable. “CNF also stands for ‘carbon neutral fiber’ It can be produced using the infrastructure of the paper industry,” he says enthusiastically.
As the need for a shift to a decarbonized society and the reduction of plastic waste grows, the time for CNF to make a significant leap is approaching.
#CNF #CelluloseNanofiber #Sustainability #Innovation #Mreport
Source: Nikkan Kogyo Shimbun