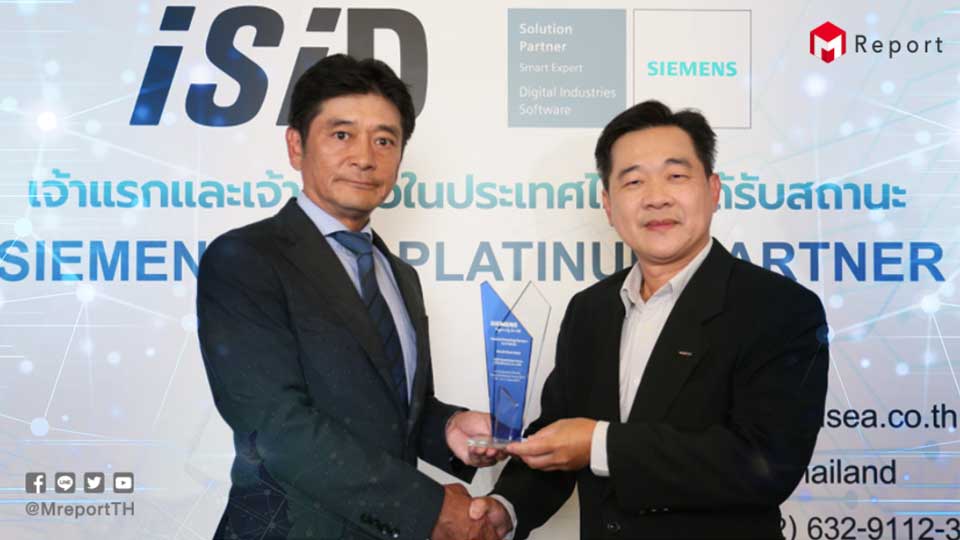
ISID Thailand emerges as Siemens PLM Platinum Partner and ready to push Thai industry toward smart factory
ISID Thailand emerges as Thailand’s first and only Siemens PLM Platinum Partner and is ready to push Thai industry toward smart factory.
Mr. Kenichi Karasawa, the ISID Thailand managing director, said, “The software technology for the manufacturing industry will play a part in accelerating its transition to a smart factory.”
On December 15, 2021, ISID South East Asia (Thailand) Company Limited and Siemens Industrial Limited - Digital Industries Software held a press conference announcing the appointment of ISID Thailand as a “Siemens PLM Platinum Partner,” in which Mr. Kenichi Karasawa, the managing director of ISID Thailand, received a plaque from Mr. Somboon Anantathanasarn, the head of software business unit, Siemens Industrial Limited. ISID Thailand is the first and only one in Thailand to receive this status. With this special alliance, the industry will fully benefit through a partnership with Siemens and ISID campaigns.
Why did ISID Thailand receive Siemens PLM Platinum Partner status?
Since 2005, ISID Thailand has brought in Siemens software to help improve the productivity of entrepreneurs in Thailand, especially in the automotive and electrical appliances industries. So it has been very well acknowledged in the industry. In 2021, another challenging year due to the coronavirus pandemic, ISID Thailand continues to strive to succeed in an automotive manufacturer’s huge project. This is the main reason why it has earned Siemens PLM Platinum Partner status.
Mr. Kenichi Karasawa said, “Our parent company, ISID Japan, was established in 1975 as a joint venture between Dentsu, one of the world's leading advertising companies, and General Electric from the United States.
ISID Japan is a pioneer of CAE software in Japan. It was also a pioneer in bringing SDRC's I-deas software to Japan 46 years ago. The I-deas software has developed into the 3DCAD “NX” program and its successor is Siemens.”
With experience working with Siemens software, which has gone through a long period of software development, ISID has the knowledge and skills to take full advantage of the software and to bring factories through the transition for smooth software deployment.
Being recognized as a Siemens PLM Platinum Partner, ISID Thailand will enhance the competitiveness of the Thai manufacturing industry. Both Siemens' extensive experience of successful global customer service and ISID's rich knowledge will help solve problems and get the manufacturing industry accelerated to the smart factory, especially during the time when the optimization of complex production plans is ever more needed.
Mr. Somboon Anantathanasarn said, “Achieving Siemens PLM Platinum Partner status reflects our earnest desire to support Thai entrepreneurs and our readiness of qualified personnel.
ISID has helped customers acquire Siemens products, for which we provided support in design, planning, and production with software including NX, Teamcenter, Tecnomatix, Opcenter Advance Planning and Scheduling, MindSphere, and many more.”
Siemens software’s superiority
Over the past 15 years, Siemens has invested more than 10 billion euros in industrial software to become a leader in both automation and digitalization. Siemens is recognized for its engineering excellence, innovation, and reliability.
Siemens is the only company that can provide its customers with end-to-end solutions, ranging from product development process software, CAD/CAM, engineering simulation in mechanical and electrical fields, and digital twins.
Therefore, Siemens PLM Software covers all processes in the manufacturing industry, from product design to production. This is the product of the company's software development, drawing on the accumulated experience of leading the world's leading manufacturing businesses.
Siemens software is used not only in the assembly industry but also in other manufacturing industries. This is a testament to what sets Siemens software apart from others on the market.
Its strength is the compatibility between 3D CAD NX and PLM Teamcenter. It offers outstanding performance not limited to mechanical design, but also supports electrical system design and software.
In addition, Siemens software has the potential to respond to the era of digital transformation (DX), where customer needs are changing constantly and rapidly. They will enable entrepreneurs to manufacture products that meet market demand while allowing for a flexible production line, thereby supporting multiple productions and the rapid development of new products. The Xcelerator software also supports manufacturers with digital twins, production, and productivity.
Challenges to becoming a smart factory
Today, amid a wide range of fast-changing things, traditional manufacturing enterprises will not be able to survive in the market if their competitors adapt first. Those who recognize this problem are the first ones to adapt the production to become a smart factory by bringing in digitalization technology and other new technologies to use in their enterprise.
Mr. Somboon said, "In the past, we heard that "big fish" eat "small fish," but now it has become "fast fish" eat "slow fish."
The industries that need to adapt are those that are highly competitive and change rapidly.
The trend of transforming into a smart factory is evident in the automotive industry, personal appliance industry, food industry, and electrical and electronic industries, both in Thailand and abroad. The majority of Siemens customers have already transformed.
Therefore, industrial entrepreneurs must realize the necessity of converting their traditional production in order to compete with other entrepreneurs. After recognizing this trend, entrepreneurs will start to figure out their standpoint and what to do to be more competitive.
Mr. Kenichi Karasawa said, “In the transition to a smart factory, the most common mistake is that the company's management recommends that the production line install IoT technology without clearly defined objectives and KPIs. The IoT implementation may end up just as a tool to monitor the state of the production line's machines, energy consumption, etc., with no further enhancement to make the IoT investment more worthwhile.
To transition to a smart factory, entrepreneurs need to set clear objectives over the next 5 to 10 years.
In addition, what is important to the Thai economy are the small business entrepreneurs. The more money SMEs can generate, the greater the impact on the Thai economy. Currently, software vendors have developed a business model of subscription that will become an important trend, allowing SMEs to invest more easily and conveniently than before.”
Transitioning to a smart factory is a continuous development process in which entrepreneurs can begin with the most important aspect of their business today and then progress to other areas. What must be considered is the integration of various solutions to support future continuity.
ISID Thailand emerges as Siemens PLM Platinum Partner and ready to push Thai industry toward smart factory