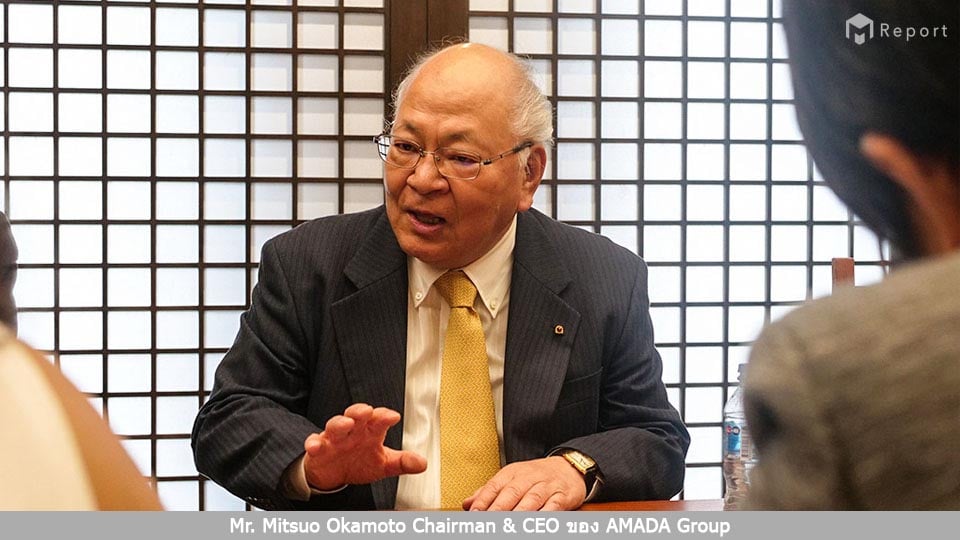
Special Interview of Mr. Mitsuo Okamoto, CEO of AMADA Group
On the occasion of AMADA ASEAN Technical Center’s 1st Anniversary, their customers and media in the ASEAN region were invited to visit the Technical Center. Mr. Mitsuo Okamoto, Chairman & CEO of AMADA Group, unveiled his vision and strategic policies of driving his next-stage business.
AMADA’s Business
Our company is a Japanese machine manufacturer of metal working applications, established in 1946. Up till now, the company has been in operation for 73 years. I have assumed the position of Chief Executive Officer since 2000, and have seriously expanded our business into international markets. Currently, there are 90 group companies globally, with total sales of 300 billion yen.
AMADA’s products include sheet metal fabrication machines, generating up to 70% of total business. Others are machine tools and precision welding machines.
Interest in the ASEAN’s Region
We are interested in the region with a high population as there will be impressive economic growth. The demand for sheet metal fabrication will arise in accordance with the expansion of a city or a residence, like the construction of buildings and other infrastructures. This is because products which are associated with sheet metals are often utilized in daily life. Our machines, as an instance, can be used in elevator manufacturers. Therefore, the ASEAN region has a high potential to generate high sales volumes.
Why was Thailand selected to be the location of AMADA ASEAN Technical Center?
Regional Head Quarter or RHQ was previously our regional headquarters, situated in Singapore. In August 2016, it was moved to Thailand, and AMADA ASEAN Technical Center was also established here, officially operated in April 2017. The three main businesses were then combined together: sheet metal fabrication, machine tools and precision welding machine.
The decision was made because we found Thailand’s potential both in its business opportunity and in its readiness to be established as the center in the ASEAN region. In addition, Thailand’s market is considered to be of high potential. Regarding sales volumes, we received a large number of orders for automated machines and high accuracy machines last year, which proves our judgement.
How important is the Technical Center?
With our strategy to have the business driven by engineering, the Technical Center becomes a significant tool as it will enable our customers and staff to learn and practice dynamic technology as well as enable us to offer good solutions to the customers with our strong engineering knowledge and experiences. This is in line with AMANDA’s statement, “Customers’ success is ours.”
What is AMADA IoT V-factory?
AMADA IoT V-factory was invented in 2015 from the concept of factory reform to Industry 4.0, starting from complete and clear visualization. V-factory will create new values for customers in 2 main portions: IoT product, converting the typical production lines to IoT smart factory, and IoT support, maintaining the efficient operation of factories by connecting AMADA and customers.
Followings are significant contents that support our customers through AMADA IoT V-Factory:
- Factory Monitoring. With IoT we can find various information like machine operation, machine condition and production consumption. Through accurate visualization, we can manage promptly anywhere in the world.
- Manufacturing Design. This is the software that creates a smart program for the entire production process to efficiently drive the smart factory.
- Factory control that creates smart schedule. This makes the entire factory highly efficient by visualizing factories and grasping the current state of machine operation, eliminating the bottleneck in the factory.
- IoT Service. By grasping the machine condition through the network, preventive maintenance is possible. In case the machine has an alarm, AMADA IoT Support Center can remotely connect to customer’s machine to identify the cause and arrange for replacement of parts as well as appointment of service staff. This is considered smart recovery in minimum time.
- IoT Consult. AMADA will conduct data analysis and make various suggestions for further improvement to completely support customers and assure data security.
In this event, we would like to introduce “My V-factory”, a new IoT product and application, which is the first step to AMADA IoT V-factory. By installing one communication device called “V-factory Connecting Box or VC Box”, we can collect all necessary information from the machine, connecting the data to the cloud. As a result, we will be able to check the information anywhere anytime through My V-factory web application by simply using a computer, a tablet or a smartphone. Anyone involved in the production, from managers to operators, can share the same information and efficiently use it together. Production efficiency and operation results of each process can be promptly assessed against the plan.
Truly connect the operations of the entire system
AMADA provides a comprehensive sheet metal fabrication (Cutting-Bending-Joining) machine for fabricating one finished product. Prior to the global spread of Industry 4.0, AMADA used the technology called VPSS (Virtual Prototype Simulation System), which enabled the installation of IoT into a machine in order to connect the operations of the entire process.
AMADA’s operational method reform with VPSS has started since 2000. The VPSS concept is to create a program for the entire fabrication process with virtual simulation to prevent mistakes and reduce the setup time. The core network technology is utilized to see the real- time operation conditions in the factory.
Technology from the Total Solution concept
We have committed to develop technology that can provide various complete solutions, called Total Solution. AMADA has developed automation systems for over 35 years, especially in bending automation, which is influenced by safety issues. It is therefore a good consideration to change the bending work from human to robot. We have also created a wide variety of solutions and functions to fully utilize this bending automation to suit different conditions and requirements. At the same time, our system can offer stable production and stable high quality. It is easy to set up and programmed, and even supports small lots of production. In addition, the system is flexible for various product shapes.
Another example of the Total Solution technology is the combined automotive cutting or punching system, called integrated process. We also offer innovations to reduce secondary and human-operated processes, and combine them with our latest technology such as a fiber laser machine as well as a combination punch and laser machine with the part taking-out and sorting system. This includes automation material storage that can customize to meet different customers’ requirements.
All of this is the design under the concept of Total Solution covering the entire fabrication process, from programming to the finished parts. This is what we have done up till the present time.
The Future of Manufacturing Industry
The improvement of manufacturing industry is called “Monozukuri” in Japanese. In my view, we, from now on, will develop our operation environment to be in line with that in developed countries, by increasing the number of machines and automation systems and reducing the amount of operator’s working time while the productivity becomes higher. This is because our current working environment is not satisfying though a big nation like China has been trying to make development for this issue. The labor cost which increases over 10% a year causes the increase in total cost. It is therefore unavoidable to utilize automation system as well as develop safe machines that even women or the ones who are over 60 years of age can safely operate. The system will be connected throughout the factory to enable continuous operation, reduce lead time and avoid operational bottlenecks. This can also cope with possible changes in business models such as business acquisition or merger. As an instance, a manufacturer of electronic parts may acquire the ownership of an auto manufacturer so that it will be able to manufacture the products that it cannot do by itself. Moreover, this can increase the capability to change business according to global trend, such as a gas firm that converts its business into a charging station.
Performance Forecast
We have set our 3-year mid-term target at 30% growth. For the ASEAN region, we expect double growth, driven by the demands in automation systems and high-end machines. The Technical Center will be the main device to accelerate these demands.